GDA350 omniflow
Self-levelling screed mortars
Toepassingen
GDA350 omniflow is een voorgemengd en industrieel vervaardigde Calciumsulfaat-gebonden gietvloermortel voor het machinaal verpompen. Door de uitstekende warmtegeleiding ideaal geschikt voor (dunne) dekvloeren met vloerverwarming. Voor laagdikten, hechtend vanaf 20 mm en zwevend op isolatie vanaf 30 mm. GDA350 omniflow dient altijd te worden afgewerkt met een vloerafwerking. Voorbeelden van binnentoepassingen zijn o.a. woning- en utiliteitsbouw.
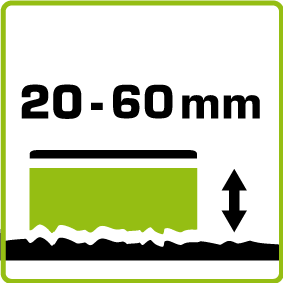
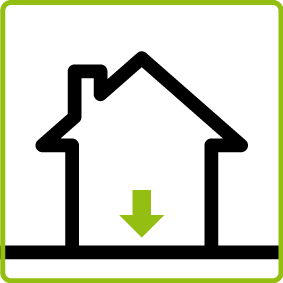

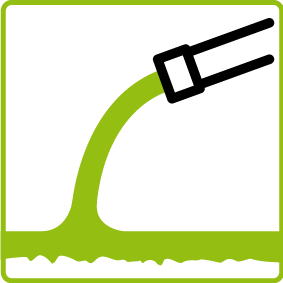
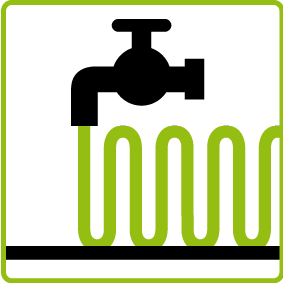

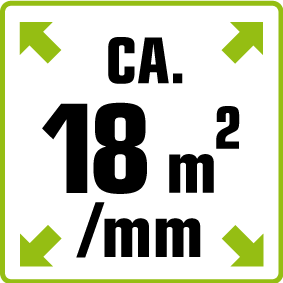
Getting started with GDA350 omniflow
Certificates and documents
Download the documents available from this specific product here.
Additional documents
Can't find the right certificate?
Contact usLet us help you out
Why is it important to prepare the surface?
- you can often finish it with a simple primer.
- OR you may have to further remove the surface, for example in the case of loose parts.
- OR you still have to pre-process by so-called dust-free “shot blasting”. This removes the top layer and any contamination from the surface and "roughens it", or increases the surface area for better adhesion. Excellent for all kinds of leveling compounds and screed floor mortars to adhere to.
How do your cast screed floor mortars differ from those from construction?
Omnicol Flooring's cast screed floor mortars are characterized by high compressive strength and fast drying. This makes them extremely suitable for use in rapid construction concepts or small (home) renovations. So that the floor can be put back into use as quickly as possible. A time saving of 80% compared to standard solutions is quite normal with our cast screed floor mortars. The higher strength makes it possible to be poured ultra-thinly onto underfloor heating systems. This results in more efficient heat transfer and the floor warms up very quickly. The ultimate solution for underfloor heating systems, where efficient heating and delivery are key.
What temperature should the subfloor be during leveling?
During processing it is necessary to keep the temperature of the subfloor, space and material between 15 °C and 25 °C. In addition, the relative 65% of the lager must be before, during and a few days after maceration!